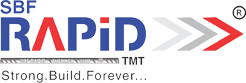
One of the fundamental characteristics of materials is their ductility, which is the capacity to undergo deformation under stress without breaking. Because of this special quality, materials can experience extensive plastic deformation before failing, which makes them essential for a wide range of technical applications. Designing components and structures that can bear mechanical loads without catastrophic failure requires an understanding of ductility.
Ductility describes a material’s ability to elongate or stretch under tensile tension before breaking. During tensile testing, it is frequently expressed as a percentage of cross-sectional area decrease or elongation. Unlike brittle materials, which fracture with little distortion, ductile materials show considerable plastic deformation before the failure.
It affects the mechanical behavior and structural integrity of materials and components, ductility is significant. Here are some major justifications for why ductility is important:
Structural Flexibility: Under load, structures can bend and flex without breaking because ductile materials can experience significant deformation before failing. In applications like earthquake-resistant structures and automobile accident safety, this flexibility is crucial.
Forming Ease: Ductile materials are easily formed and shaped using techniques like extrusion, forging, and rolling. In the manufacturing sector, this quality is crucial for creating intricate parts with exact geometry.
Resistance to Fracture: Ductile materials’ capacity to flexibly shift stress concentrations lessens the chance of abrupt fractures. They are therefore appropriate for applications with dynamic or varying loads.
Energy Absorption: Impact-resistant constructions and safety equipment like helmets and bumpers benefit from ductile materials’ ability to absorb energy through plastic deformation.
Machinability: Because ductile materials show uniform deformation rather than abrupt fracture, they are typically easier to process than brittle materials. Tool life is increased and manufacturing procedures are made simpler by this feature.
Many materials are ductile to different extents; some noteworthy examples are as follows:
Metals: Because of their metallic bonding structure, which permits atoms to slide past one another under stress, many metals are intrinsically ductile. Typical ductile metals are steel, copper, aluminum, and gold. The electrical, automotive, aerospace, and construction industries use these metals extensively.
Alloys: By altering the microstructure and mechanical characteristics of metals, alloying elements can increase the ductility of metals. For instance, steel is created when iron and small amounts of carbon are combined. Steel has better ductility than pure iron. The ductility of different metal alloys is also influenced by other alloying elements such as manganese, nickel, and chromium.
Polymeric Materials: Some polymers, especially thermoplastics like polyethylene, polypropylene, and polycarbonate, have ductile properties. These materials are appropriate for use in consumer goods, tubes, and packaging because they can experience substantial elongation and distortion when subjected to tensile stress.
Ceramics: Although they are typically thought of as brittle, certain ceramic materials can behave ductilely in certain situations. Ceramics made of silicon carbide and silicon nitride, for example, may show restricted ductility at high temperatures or under specific loading circumstances.
Composites: Depending on their component materials and manufacturing processes, composite materials made of a mixture of fibers and matrices may have ductile behavior. Fiber-reinforced composites, including carbon fiber reinforced polymers (CFRP), are preferred for use in sporting goods, automotive, and aerospace industries because they frequently have great strength and ductility.
Ductility is one important mechanical characteristic that affects how materials behave and function in various engineering applications. Designing and choosing materials that satisfy the particular needs of many industries requires an understanding of the meaning, significance, and applications of ductile materials. Ductile materials—from metals and alloys to polymers and composites—are essential to forming the contemporary world and promoting technological advancement.