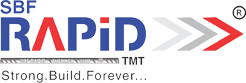
In the world of construction, selecting the right materials is a key factor in ensuring the strength, durability, and longevity of a structure. Among the most crucial materials used in building frameworks are TMT bars, which provide the necessary reinforcement for concrete structures. To make an informed decision about which TMT bars to use for your project, it’s essential to understand both the different grades available and the TMT bar manufacturing process.
This article will explore the grades of TMT bars, explain how they differ, and provide insight into their manufacturing process. We’ll also discuss the advantages of using TMT bars in construction and how SBF Rapid ensures the highest standards of quality in their production.
Before diving into the manufacturing process, let’s first understand what TMT bars are and why they are vital in construction. TMT stands for Thermo-Mechanically Treated bars. These are high-strength reinforcement bars with a soft inner core and a tough outer surface, which give them a unique combination of strength and flexibility. TMT bars are widely used in reinforced concrete structures such as buildings, bridges, and other infrastructure due to their ability to bear heavy loads, resist earthquakes, and withstand fire.
At SBF Rapid, we specialize in providing premium TMT bars that meet the demands of a variety of construction projects. Our bars are produced through a meticulous TMT bar manufacturing process, ensuring that each bar meets industry standards and performs optimally in all conditions.
The TMT bar manufacturing process is a highly technical and sophisticated procedure that involves multiple stages. This process is what gives TMT bars their distinct properties of strength, flexibility, and resistance to external factors such as corrosion, earthquakes, and fire. Here is a detailed look at the steps involved in manufacturing TMT bars:
The process begins with the extraction of raw materials such as iron ore, coal, and limestone. These materials are mined and then processed in blast furnaces to produce molten iron. This molten iron is then converted into steel by removing impurities like carbon and sulfur through various refining methods.
Once the impurities are removed, the purified steel is cast into long rectangular blocks known as billets. These billets serve as the raw material for the next phase of the TMT bar manufacturing process. SBF Rapid ensures that the billets used in our TMT bar production are of the highest quality to guarantee the final product’s durability and performance.
The billets are then heated to extremely high temperatures (around 1100-1200 degrees Celsius) and passed through a series of rolling mills to form them into bars. During this stage, the steel bars take on their characteristic ribbed design, which enhances their bonding strength when embedded in concrete.
After the bars are rolled into the desired shape and size, they undergo a process called quenching. Quenching is a critical step in the TMT bar manufacturing process that involves rapidly cooling the bars using water jets. This cooling process forms a hard, martensitic layer on the outer surface of the bar, giving it the strength needed for structural reinforcement. Meanwhile, the core remains softer and more ductile, providing the flexibility required to absorb seismic shocks and other forces.
The bars are then subjected to self-tempering, which is a natural process that occurs due to the residual heat present in the core. This heat causes the outer layer to temper, resulting in a strong and tough bar with a ductile core. Self-tempering enhances the bar’s ability to resist both high pressure and dynamic forces, making it ideal for high-stress applications.
In the final stage, the bars are cooled under atmospheric conditions to allow for uniform distribution of temperature across the bar. This cooling process is crucial in ensuring the bar’s structural integrity and maintaining the balance between its strength and flexibility.
The result of this detailed TMT bar manufacturing process is a product that offers high yield strength, superior ductility, and excellent resistance to natural elements, such as earthquakes and corrosion. At SBF Rapid, our manufacturing process is carried out under strict quality control standards to ensure that each TMT bar meets the requirements for various construction applications.
TMT bars come in different grades, each with its specific set of properties suited to various types of construction projects. The grades are designated by their yield strength in megapascals (MPa), with the most commonly used grades being Fe 415, Fe 500, Fe 550, and Fe 600. Let’s take a closer look at the characteristics and applications of each grade.
Fe 415 TMT bars are the most basic grade available, with a yield strength of 415 MPa. These bars are often used in small-scale construction projects such as residential buildings, villas, and low-rise structures. They provide good ductility and flexibility, which makes them ideal for areas that are not prone to heavy seismic activity.
Applications:
Advantages:
Fe 500 grade TMT bars are the most widely used grade due to their balance of strength and ductility. With a yield strength of 500 MPa, they are suitable for both residential and commercial construction projects. Fe 500 TMT bars are particularly popular in earthquake-prone areas due to their flexibility and ability to absorb seismic energy.
Applications:
Advantages:
With a yield strength of 550 MPa, Fe 550 grade TMT bars are stronger than Fe 500 and are often used in industrial and infrastructure projects. These bars are designed to withstand higher loads and are ideal for heavy-duty construction where strength is a primary concern.
Applications:
Advantages:
Fe 600 grade TMT bars offer the highest yield strength at 600 MPa. These bars are typically used in large infrastructure projects such as bridges, dams, and high-rise buildings where maximum strength is required. Their high tensile strength makes them the go-to choice for projects that need to bear heavy loads and extreme environmental conditions.
Applications:
Advantages:
At SBF Rapid, we offer a comprehensive range of TMT bars in all grades to meet the specific needs of any construction project, from residential homes to large infrastructure undertakings.
TMT bars have several advantages that make them the preferred choice in modern construction. These benefits stem from the unique TMT bar manufacturing process, which gives them superior strength, flexibility, and resistance to various environmental factors.
One of the most significant advantages of TMT bars is their ability to withstand seismic forces. Thanks to their flexible core, TMT bars can absorb the energy from earthquakes without breaking, making them an essential component in buildings located in earthquake-prone regions.
TMT bars are highly resistant to corrosion, which is especially important for structures located in coastal areas or regions with high moisture levels. The quenching process in TMT bar manufacturing ensures that the bars have a protective oxide layer that prevents rusting.
TMT bars can withstand temperatures as high as 600 degrees Celsius, making them highly fire-resistant. This characteristic adds an extra layer of safety to structures in case of fire accidents.
The combination of a hard outer surface and a flexible core gives TMT bars their superior strength and durability. This makes them suitable for high-rise buildings, industrial projects, and large infrastructure.
While TMT bars offer superior strength and durability, they are also cost-effective. Their high strength allows for the use of fewer bars, reducing the overall cost of the project without compromising on safety or stability.
TMT bars are an integral part of modern construction, providing the necessary reinforcement to ensure strength, durability, and safety in buildings and infrastructure. Understanding the different grades of TMT bars and the TMT bar manufacturing process is crucial for selecting the right material for your project.
At SBF Rapid, we take pride in offering high-quality TMT bars that meet all industry standards. Our manufacturing process is designed to produce TMT bars that are strong, flexible, and resistant to environmental factors, ensuring that your construction project stands the test of time.
Whether you are working on a residential home or a large infrastructure project, SBF Rapid has the right grade of TMT bars to meet your needs. Reach out to us today for more information on how we can support your construction efforts with our top-tier TMT bars!